Worldwide, thousands of municipal wastewater treatment plants rely on NOV Fiber Glass Systems piping products every day to keep their communities serviced efficiently and reliably.
NOV Fiber Glass Systems has a 60-year proven track record in wastewater treatment plants where our glass-reinforced epoxy (GRE) piping products have been installed in a variety of critical processes:
- Activated waste lines
- Chilled water
- Demineralized water
- Ferric chloride
- Ferrous chloride
- Fuels
- Grit piping
- Hot air (denitrification)
- Hot water
- Hydrochloric acid
- Incinerated ash slurry
- Odour control
- Polymer
- Potable water
- Primary sludge
- Raw sewage lift stations
- Return activated sludge
- Scum
- Secondary containment systems
- Sewage
- Sodium hydroxide
- Sodium hypochlorite
- Solvents
- Sulphuric acid
- Thickened waste activated sludge
- Treated sewage
- Waste activated sludge
- Waste heat recovery
GRE’s composite construction of aromatic amine cured epoxy resin and premium glass fibre reinforcement produces a piping system with an unmatched strength:weight ratio when compared to thermoplastics or less advanced composites such as glass-reinforced vinyl ester. Our products have been tested for suitability from -180°C–149°C (-292°F–300°F) in a wide range of chemical applications and are available with pressure ratings up to 240barg (3500psig).
Scale and struvite resistance
NOV Fiber Glass Systems’ GRE piping products feature a pipe bore with a Hazen-Williams coefficient of C=150 that makes it highly resistant to scaling and struvite. Like other products, struvite will build up in dead legs and areas with low or stagnant flow; however, resulting buildup is easily removed by pigging or hydroblasting. With very few nucleation points for scale to form, our products consequently resist struvite and scale deposition.
A case study was conducted in a North American wastewater treatment plant to compare the scale and struvite resistance of NOV Fiber Glass Systems Green Thread HP® GRE piping to steel piping. The two materials were installed as new, back-to-back in the same sludge service. Upon inspection it was noted that Green Thread HP16 had substantially less struvite deposition in the pipe. Maintenance activities for the facility operators have been substantially reduced everywhere that Green Thread HP16 has been installed.
Corrosion resistance
NOV Fiber Glass Systems’ GRE piping eliminates both internal and external corrosion. Furthermore, when piping is insulated, the concerns associated with corrosion under insulation are also mitigated.
Because GRE is nonmetallic, requirements for cathodic protection, anodes and corrosion inhibitors that would be required for a steel piping system are eliminated. Similarly, GRE is not affected by (or contribute to) galvanic corrosion.
GRE does not suffer from residual elements corrosion, microbiologically-induced corrosion, and requires no coatings.
Enhanced flow properties
GRE tends to have a larger cross-sectional area when compared to steel or thermoplastics. This leads to improved pumping efficiencies and less energy required to move the same amount of water. Less head loss means smaller pumps and less energy consumption.
GRE’s Hazen-Williams flow coefficient of C=150 represents an absolute roughness that is an order of magnitude better than new steel, which contributes to substantially lower head losses. This smooth bore is maintained over the life of the pipe system thanks to the inherent corrosion resistance of GRE – the system does not suffer from the corrosion-erosion cycle like steel which reduces smoothness and increases head losses as the piping corrodes. The smooth bore also provides a significant reduction in nucleation points for scale formation – scale buildup is dramatically reduced or eliminated when compared to steel pipe.
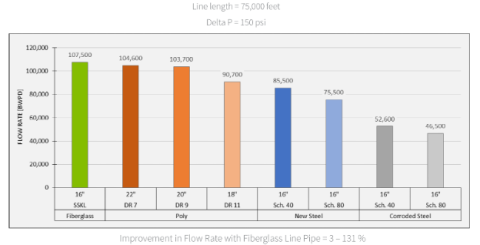
Optimized pipe rack layouts
GRE offers lower thermal end loads compared to thermoplastics or metallic piping. The high strength:weight ratio of the product means that thermal growth of long pipe runs can be managed by anchoring at the ends and guiding with intermediate supports to keep the pipe in compression and prevent buckling. This usually eliminates costly expansion joints and the layout complexities of adding expansion loops.
Because the product is lighter with lower thermal forces, supports and secondary steel requirements are simplified.
GRE offers the best spans amongst nonmetallic piping options – support spacing is reduced by at least 30% when compared to vinyl ester piping, and cut in half (or more, depending on temperature) when compared to thermoplastics.
Optimized buried piping system layouts
The low forces of expansion/thrust associated with GRE piping mean that virtual anchors can typically be utilized, eliminating the requirement for costly thrust blocks on long pipe runs.
GRE is flexible, which allows gradual changes in direction to be accommodated without the use of fittings. Long sections of pipe can be assembled next to the trench, and then roped into place using side booms or excavators.
External coatings and cathodic protection are not required for GRE pipe – bare pipe can be direct buried without the concern of external corrosion associated with steel piping.
Heat loss, insulation, heat tracing
The thermal conductivity of GRE piping is 99% lower than steel piping – a useful benefit in situations where there is an economic consequence to process fluids changing temperature from inlet to outlet in a pipeline.
Our products can be insulated in the same fashion as other materials, or preinsulated and jacketed by GF Urecon for ultimate energy efficiency. Green Thread HP16 or Star Super Seal Key Lock preinsulated with GF Urecon’s insulation system offers a piping system with virtually zero measurable heat loss from inlet to outlet, even when piping runs are many kilometers long.
When GRE piping systems are heat traced, a low-wattage self-regulating electric heat trace cable is the recommended choice.
Installation Benefits
Lighter weight – 60 – 85% lighter than steel means simplified handling.
Full QC and raw material traceability for bond (weld) mapping
Substantial reduction in carbon intensity:
Manufacturing: -31% (less energy intensive)
Transporting: -77% (lighter – more pipe/truck)
Pumping horsepower: -60% (larger, smoother bore)
System replacement: -65% (longer service life, easier to replace)
Bonded connections eliminate maintenance and leak paths at flanges associated with glass-lined steel piping.
Adhesive Technology
NOV Fiber Glass Systems is a pioneer and the recognized world leader of adhesive bonded bell x spigot and socket joint technology. Adhesives are pre-measured, kitted and ready to use: mix part B into part A, and apply. Our joining systems have been in use for over 50 years and are installer-centric, fast, repeatable and reliable.
Green Thread HP®
Aromatic amine cured epoxy resin piping featuring a resin-rich corrosion barrier for improved chemical resistance and high temperature performance.
- Available in 1” – 42” diameters.
- 16barg – 40barg (232psig – 580psig) piping classes available.
- Rated for continuous operation up to 121°C, depending on chemical service.
- Matched tapered bell x spigot joining system offered on all diameters for fast, repeatable, reliable connections.
- NSF-61 type approved.
- Canadian Registration Numbers for flanges and fittings.
- Green Thread HP is the industry standard for many applications in Canada.
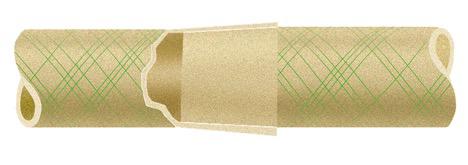
Joining system advantage – matched tapered bell x spigot
- Positive joint lock up
- Precision-ground matching tapers create a self-aligning connection
- A permanently bonded connection provides an economical, leak-free alternative to flanges.
- Can be easily field spooled by certified bonders.
Installation advantages over glass-lined steel piping
Bonded connections eliminate expensive flanges and related hardware, gaskets, and potential leaks. Bonded joints also take up much less room than flanged connections, which simplifies and reduces the size of pipe racks where multiple pipelines are running in parallel.
Spools can be made in a shop or fabricated on site. Changes can be made easily using portable field-deployed tapering tools. This allows for much better deliveries, and field flexibility for installation.
Thermal/pressure expansion and contraction is easily controlled thanks to the 96% reduction in forces associated with Green Thread HP16 when compared to carbon steel. Expansion joints and loops are usually eliminated.
Easier to remove and handle because it is 85-90% lighter.
Flanges and fittings can be added in the field by cutting, tapering and bonding without an expensive and lengthy offsite relining process.
Instrumentation outlets, vents, drains and flushing points can be added into the system at any time using bonding reducing saddles.
Green Thread HP16 is stocked in Canada, with 1 – 2 day deliveries for project adders.
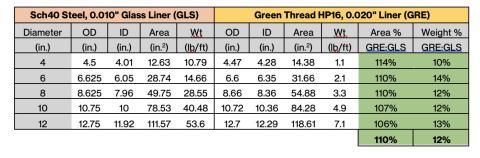
On average, Green Thread HP16 offers a 10% improvement in cross sectional flow area, and is 88% lighter than glass lined steel.
Maintenance advantages over glass-lined steel piping
Green Thread HP does not require painting to prevent external corrosion.
Green Thread flange bolt torques are very low. Re-torqueing requirements are minimized compared to steel pipe, particularly when Kroll & Ziller rubber-steel gaskets are used.
Buildups on the pipe ID can be removed with water pigs.
If needed, the lightweight nature of the product makes removal of most spools feasible by hand with no heavy equipment needed.
Long-term service tests
Raw sewage, effluent water, ferrous/ferric chloride
An Ontario, Canada wastewater plant installed Green Thread HP piping in the mid-1980s in wastewater and water treatment chemical applications. After 27 years in service, questions were raised about product integrity; 3” – 6” samples were cut out and returned to NOV Fiber Glass Systems for destructive testing. Tests of the ultimate hydrostatic hoop strength of the samples via ASTM D1599 ultimate short-term burst showed wall weeping from 106–169barg (1,550–2,450psig). This was a 10barg design product at the time of original installation! The tests proved that the hoop tensile strength of the piping is still above acceptable minimums from 1986 manufacturing ITP requirements. These piping systems are still in service, with many more years of trouble-free service remaining.
Primary sludge, waste activated sludge, return sludge, thickened waste, raw sewage
18 kilometers of 6” and 10” GRE piping were installed in a Quebec wastewater facility in 1990. The pipe pictured below on the left is before cleaning – some scale formation in the pipe bore is evident, but the ID is not significantly reduced thanks to the pipe’s smoothness and the operator’s periodic maintenance with only soft foam pigs. The pipe pictured below on the right is after cleaning – the resin-rich inner surface is still intact and virtually unaffected after 29 years in service. In 2019, the facility owners contacted Fibreglass Solutions to discuss repurposing this extensive piping system for a new biomethane process involving a higher design temperature and pressure – after 29 years, the samples (taken from service) passed;
- ASTM D1598 1000-hour test at 50barg (725psig) and 65°C (150°F) to verify condition.
- ASTM D1599 short term burst test with ultimate failure in excess of 96barg (1400psig).
- ASTM D2412 ring crush testing, with the samples exceeding the minimum stiffness factor and ring crush loads specified for contemporary manufacturing.
- Glass transition (Tg) testing, with values obtained via differential scanning calorimetry; all samples were found to be within the acceptable range specified for contemporary manufacturing.
The samples were returned to the client following the tests. Fibreglass Solutions supplied the owner and installation contractor with additional materials to extend this piping system as part of the newly-constructed biomethane facility.
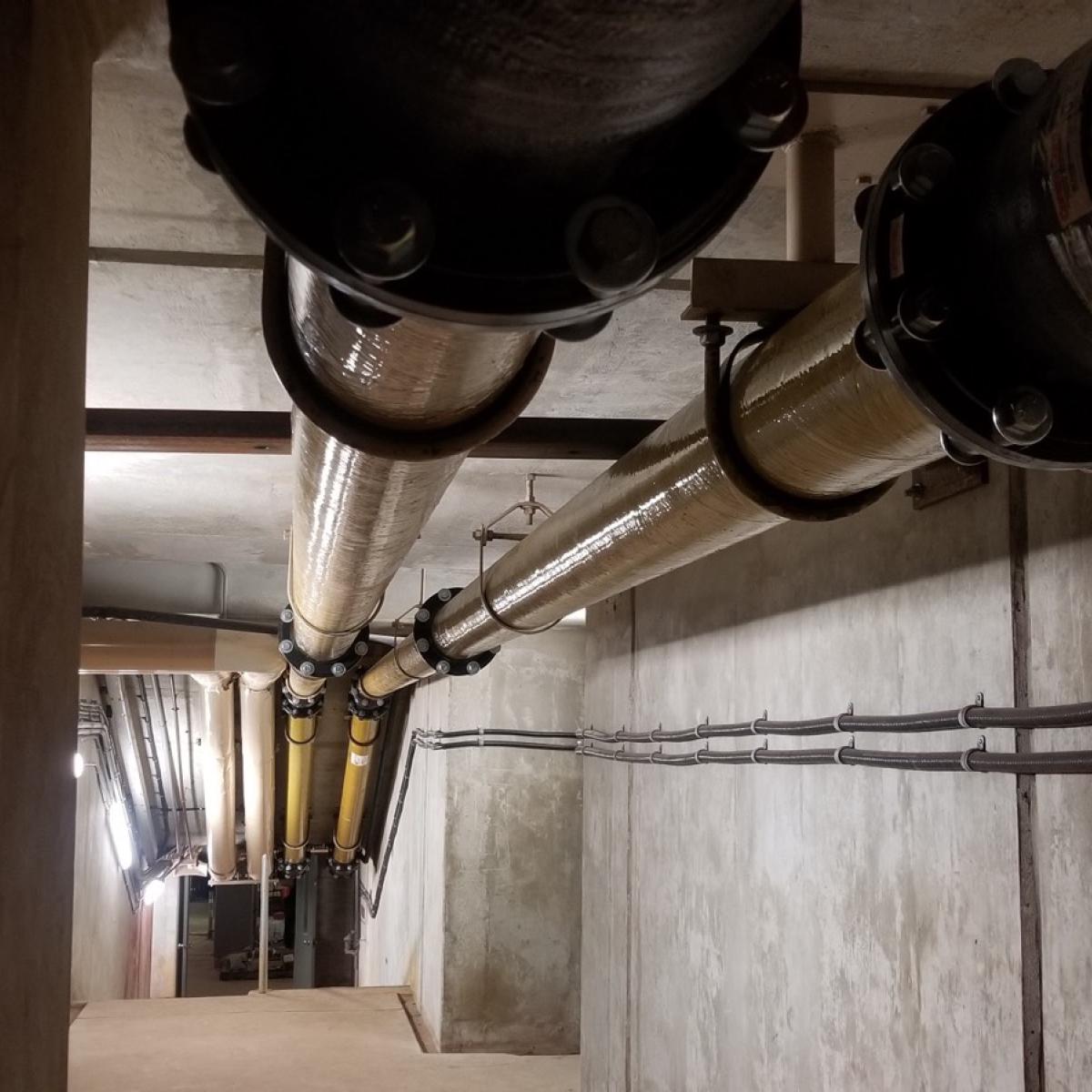